Small, nearly invisible cracks are no longer the costly threat they once were for Moroccan industrial operators. Equipped with highly sensitive and precise radiation technology, operators are now uncovering flaws before they compromise production and industrial processes — which has helped to boost production quality and save millions of dollars in maintenance and repair costs.
Small, nearly invisible cracks are no longer the costly threat they once were for Moroccan industrial operators. Equipped with highly sensitive and precise radiation technology, operators are now uncovering flaws before they compromise production and industrial processes — which has helped to boost production quality and save millions of dollars in maintenance and repair costs.
“Industrial operators used to run their facilities until unexpected breakdowns forced them to shut down for very long periods of time,” said Rachad Alami, Head of the Industrial Applications Division at the National Centre for Nuclear Energy, Sciences and Technology in Morocco (CNESTEN). “Maintenance and repair costs were very high, and this was harming competitiveness. Now nuclear techniques are used to detect problems and improve production quality.”
Moroccan industrial operators have worked with CNESTEN specialists trained by the IAEA in using non-destructive testing to inspect industrial equipment and conduct quality assurance tests. In Morocco, these techniques, which represent more than 98%of the technical controls carried out on industrial plants worldwide, have been applied in diverse branches of industry, including the petrochemical, phosphates production and processing, metal, transport, food and cement sectors.
Over the past three decades, Moroccan industry has benefited greatly from radiation technology, Alami said. While accurate figures on the savings generated by the application of nuclear technology are hard to come by, industrial operators in Morocco agree that the minimum benefit ratio for the use of nuclear techniques is 32:1 — which means that for every euro spent on non-destructive testing (NDT), radiotracers and other radiation applications, operators saw a return of at least 32 euros.
Gamma scanning helps restore petrochemical refinery operations
Conventional methods are often not precise or sensitive enough to get to the root of a problem. In 2015, engineers at a petrochemical refinery used conventional techniques to look for the reason behind a nearly 90% drop in the operation capacity of a furfural production unit (furfural is a solvent used in the manufacture of many industrial products). They could not find the source of the problem and decided they needed to dismantle the entire unit, which would halt production for weeks.
Before dismantling the unit, they decided to try a radiation technique called gamma scanning (See The Science box) to get a better idea of what was happening inside the unit and find the source of the problem. Within hours, they had identified the problem, replaced the damaged portion of the unit and restored it to full operating capacity.
“Gamma scanning was the only technique able to detect the problem and to locate it precisely,” Alami said. “It was much cheaper to use this technique — which costs € 5000 — than to sustain the huge loss that would have resulted had we dismantled the entire unit.”
Promoting radiation technology in Morocco and Africa
Specialists in Morocco are now using their decades of experience to support countries around Africa in using NDT, sealed radioactive sources and radioactive tracers. “Since the 1990s, Morocco has taken a leadership role in the application of radiation technologies thanks to the commitment of CNESTEN and support from France and the IAEA,” said Patrick Brisset, an industrial technologist at the IAEA.
Central to Morocco’s collaboration in the region is the IAEA-supported African Regional Co-operative Agreement for Research, Development and Training Related to Nuclear Science and Technology (AFRA).The AFRA programme has helped establish direct cooperation between Morocco and countries such as Angola, Cameroon, Egypt, Ethiopia, Ghana, Senegal, Sudan, Tunisia, Tanzania and Zimbabwe. As a result of this cooperation, a number of these countries have been able to implement nuclear and nuclear-related techniques in their own local industries.
“Industrialization is really taking off in many countries on the African continent. The IAEA works with countries like Morocco to promote the peaceful use of radiation technologies in industry with the aim of having an immediate impact on the countries’ economies,” Brisset said.
The IAEA, in part through its technical cooperation programme, continues to stimulate the use of these technologies and to support collaboration. Morocco has been the donor country in industrial projects involving radiation technology with the Democratic Republic of the Congo, Egypt, Kenya, Sudan and Zimbabwe.
__________
This is one of several topics that will be discussed by more than 300 experts and officials at the IAEA International Conference on Applications of Radiation Science and Technology (ICARST) happening from 24 to 28 April 2017.
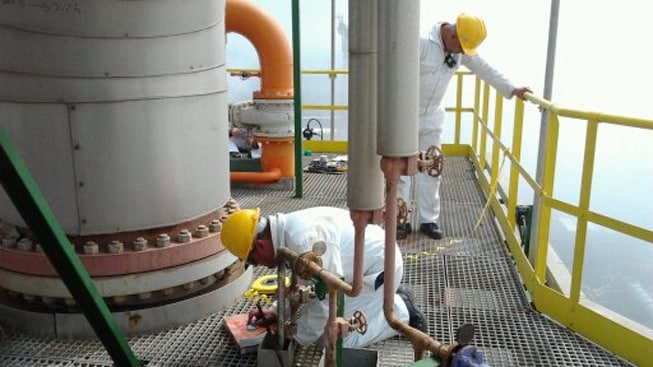
(Photo: R. Alami/CNESTEN)
THE SCIENCE
Non-destructive testing, radiographic testing and gamma scanning
Industrial testing using nuclear technology involves using ionizing radiation — along with other methods — to test the quality of materials, without causing any damage to them or leaving behind any radioactive residue. This technique is called non-destructive testing (NDT).
Radiographic testing represents the largest non-destructive testing (NDT) technique on the market and is considered to be the reference method for all other complementary techniques. It is mainly based on gamma rays from radioactive sources or X-rays from X-ray generators. Sometimes beta rays can also be used for low density, low thickness materials. When radiation is sent through a piece of material, specialists can use a special device that detects the radiation and creates an image. The higher the density or thickness of the material, the less radiation gets through, which results in less black on the image. Specialists evaluate these images to determine different characteristics of the material.
Gamma scanning is a technique used to carry out an internal inspection of any process or equipment without interrupting production. A collimated beam of penetrating rays is allowed to pass through the shell of a vessel, gets modified by the vessel internals and then comes out of the other side to reach a detector. By measuring the intensity of the transmitted radiation, valuable information can be obtained about the densities of the materials present inside the vessel. The higher the density or thickness of the material, the less radiation gets through. This leads to a simple and efficient method, a so-called ‘scan profile’ of the inspected component, which specialists can use to identify flaws or inconsistences.